Heating elements with true cold ends
Kamet supplies a range of standard individual mineral insulated resistance heating elements. Due to its high power density, mineral insulated heating elements are suitable for applications where the linear power in the heated zone is high (>100 W/m) and the cold ends can go through insulated walls without the concern of overheating.
These are available as one-wire heating elements (our internal reference CVX and CXX heaters) and two-wire heating elements (our internal reference BVX and BXX heaters). These heaters offer flexibility to our customer due to its various mounting options to match their specific application for example, coiling, clamping or brazing.
Product summary
- Seamless hot/cold transition over heater length
- Ease of termination due to conductive cold end
- High power density
- Heats up to 1000°C
- Suitable for a wide variety of applications
- Standard sizes available from stock
One-wire and two-wire MI heating elements
Mineral insulated heating elements consisting of one/two current-carrying conductors, insulated with magnesium oxide (MGO) and protected with a flexible metal sheath that has a minimum bending radius of 2x the outside diameter.
These mineral insulated (MI) heating elements are equipped with a conductive cold end, typically from materials like copper or nickel, which possess significantly lower resistance values. This design facilitates easy termination by ensuring the cold end can seamlessly integrate into various setups.
This cold end has a internal/seamless hot/cold transition. Meaning there is no difference in outer (sheath) diameter where hot and cold elements meet. The sheath is electro-etched where internal hot/cold splices are located.
The cold end facilitates straightforward termination, often achieved through the use of metal-to-ceramic connectors. The primary distinction between one-wire and two-wire heating elements lies in their termination requirements: one-wire heating elements necessitate termination at both ends, whereas two-wire heating elements require termination at just one end, thanks to the circuit formed by the two wires.
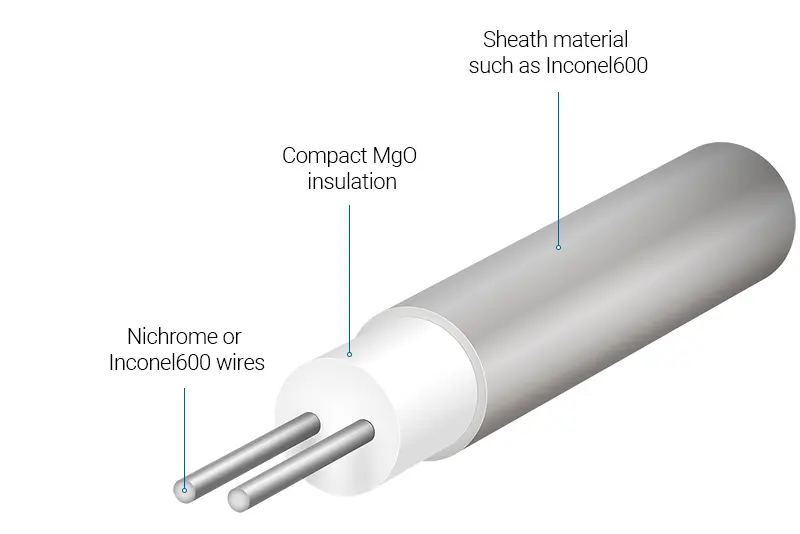
Specifications and physical properties
Physical properties
- Sheath: Inconel® 600 standard 304SS, 316SS, or 321SS on request
- Insulator: ≥99.4% Compacted MgO
- Hot Wire: Inconel® 600 standard. Nichrome 80/20 on request
- Cold Wire: Copper (one-wire), Nickel (two-wire)
Maximum working temperature
- Hot Part: 1000⁰C
- Cold Part: 300⁰C (one-wire), 300⁰C (two-wire)
Tolerances
- Sheath Diameter: +0/-0.08mm
- Hot Section Linear Resistance: ±10%
- Hot Section Length: <1500mm; +0/-10% ≥1500mm; +0/-7%
Industrial applications
MI heating elements excel in heating liquids, gases and vacuum applications:
Heating Liquids or Gases
Exploring the intricacies of heating liquids and gases reveals a world where precision meets practicality. Each method, whether submerging elements in liquids or coiling them for gas heating, is designed with specific power and temperature limits in mind. Kamet’s expertise shines in offering solutions that adapt to the dynamic nature of these fluids, ensuring efficiency and safety. Here’s a closer look at these methods and their technical specifications. Based on our experience, two-wire heating elements are more commonly employed in the heating of liquids or gases. For liquids, the heating elements are submerged into the liquid. In the case of gases, the heating elements are typically coiled around a cylinder, as seen in applications like gas chromatography.
Heating liquids
- Submerge directly in the liquid to be heated
- Maximum power density: <9 W/cm^2 for standing liquid
- Maximum temperature: 980⁰C
NOTE: For applications with fast moving liquids, power density can be increased. Contact Kamet for advice in this regard.
Heating gases
- Commonly coiled and inserted inside a tube where gas moves over the coils or as oven heating element for harsh environments
- Maximum power density: <4.5 W/cm^2 for standing air
- Maximum temperature: 980⁰C
NOTE: For applications with fast moving gases, power density can be increased. Contact Kamet Trading to consult.
Heating in vacuum environments
Radiant heat is one of the most common methods of heat transfer in a vacuum. Electric heaters need to be over 500°C before metal surfaces start to radiate heat away from the surface of the heater. Keeping that heat in the area of the process and away from the cold section of cable brings a new generation of efficiency to radiant vacuum process heating. The desired heating rate and required power will determine the mounting method. Vacuum applications bring particular challenges:
- A vacuum acts like a heat trap. Until radiant temperatures are achieved the heat stays in the heater or the parts that are being heated.
- Sensing temperatures from metal heater surfaces in a vacuum can also be difficult.
NOTE: For increased life time or heating uniformity, brazing or casting is recommended even if < 4.5 W/cm^2
Brainstorm with an expert about your heating needs
How can we help you today?
"*" indicates required fields
Mounting methods for MI heating elements
Heating elements can be mounted onto all kinds of materials. Due to its flexibility, the heaters can be bent in several shapes to transfer heat effectively.
The chosen mounting method depends on the desired heating rate and required power. The table below contains information on the parameters of various mounting methods for the mineral insulated heating elements.
Wrapped around an object
Coiled inside an object
(Vacuum) brazed on panel
Fixed with welded brackets
Held together by a clamp system
Power Density W/cm^2 | Temperature ⁰C | Mounting Method |
---|---|---|
< 3 | < 980 | Simple wrap & loose clamping is acceptable |
3 – 6 | < 300 | Simple wrap & loose clamping is acceptable |
3 – 6 | 300 – 600 | Must be clamped tightly to the object |
3 – 6 | 600 – 980 | Must be partially brazed, spot welded or cast into the piece to be heated |
6 – 15 | < 980 | Must be completely soldered, brazed, or cast into the piece to be heated |
Why work with Kamet?
Through partnering with ARi, we offer extensive testing and services, including vacuum brazing, which integrates the heater into the customer’s specified material. Vacuum brazing creates clean, strong joints that resist thermal and mechanical stress, crucial for the durability of heating elements. This process heats the assembly evenly, leading to uniform expansion and contraction. This uniformity benefits complex shapes and assemblies by reducing the risk of thermal distortion.
Here are other key features of Kamet that our loyal customers appreciate:
- Our team speaks multiple languages.
- We respond quickly and communicate clearly.
- We are reliable and innovative problem-solvers, and we offer transparency about our partners and manufacturing process.
- The heater junctions are laser welded to ensure top-notch quality.